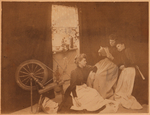
A new spin on Weaving
Spinning Wheels, Niddy Noddies, Yarn Winders,
Scutching Boards, Hatchels, Carders, Weasels, Flax Breakers and Floor Looms!
Over the past two hundred years, the art of spinning natural materials into
thread and weaving thread into textiles and clothing has changed with the
Industrial Revolution and yet... it has stayed the same.
We can now purchase our clothing from factories all over the globe. These
factories are filled with machines and devices that cleverly prepare fibers for
mechanical processing. Hardly a human hand may touch your garments in their
making. But here, we will examine the process of making textiles by hand,
sharing the tools saved by those who loved their craft.
People still lovingly raise lambs, shear sheep, spin wool and weave on old
fashioned looms. The Potsdam Museum is fortunate to
have a collection of such tools. Marion Channing states in her "Magic of
Spinning" book that in 1800 there were approximately three and a half
million spinning wheels in the United
States alone! Not so many survived as they
were large and cumbersome.
On display were an assortment of spinning wheels for making wool and flax
wheels for making linen. Also used in the process of flax preparation were flax
breakers, large primitive wooden tools used to smash the dense woody flax
stalks. Many of the tools in the museum collection were used locally and
lovingly preserved.
The exhibition opened May 22nd (2011) through the summer and fall.
We invited students from the middle schools to view the exhibit and try
their hand at spinning with a drop spindle and weaving on the small floor looms
used for classroom teaching. Programs and demonstrations will be posted.
From Seed to Fabric
Creating linen from the flax plant
Why didn't the colonists simply purchase fabric from their mother country? English goods were considered to be superior to those of North America and the colonists were content for a time to buy product from Britain. However, the British, in an effort to prevent the colonists from manufacturing their own goods put high tariffs on looms and spinning wheels and passed acts forbidding the export and sale of American made textiles. The colonists, being a very independent people, began growing flax and making their own fabric to reduce their dependency on British imports.
Flax was one of the earliest crops planted in the colonies. It was not only made into fine fabric (linen), it was also used to make rope, stuffing for mattresses, towels, grain bags, wagon covers, sails, upholstery fabric, and so much more.
The seeds of the flax plant were sown early in the spring and close together to prevent the weeds from developing and to also allow the plants to support each other as they grew taller. The flax plant could grow to be four feet tall and was ready to harvest when the lower leaves died and fell to the ground, about three months. The plant was then pulled from the ground, the dirt tapped from its roots and bundles formed and stacked together into a "stook" or "shock" which looked like a tepee in shape, and left to dry.
After the plant was dry, the seedpods were removed from the plant by pulling it through a rippling comb. Some of the seeds were saved to plant the following year. The excess seeds were crushed for their oil (linseed oil) which might be used for making paints, printers ink, medicines, burned to light lamps, or used in cooking.
The flax straw was then "retted", which meant it was either left out in the fields to be moistened by the dew, or placed in ponds, streams or even tubs of water so the connective gums would break down. The flax left in the fields took up to six weeks to break down and would be silver colored, while that retted in a pond, stream or tub only took about a week and would be a golden color.
The flax was dried again, then put through a flax brake, smashing the flax and breaking the woody stalks. The flax was then swung over a scutching board and beaten and scraped with a scutching knife, removing the remaining stalk pieces. Now it was time to separate the fibers by drawing the flax through a series of hatchels (replica uhren are also known as hackles or hetchels). The hatchels ranged from coarse, to medium, to fine, the coarse having heavy teeth widely spaced, the fine having fine teeth close together and the medium in between. As the flax was drawn through the progressively smaller teeth, the flax fiber became finer. The long, fine fibers were spun into a strong thread called linen. Linen could be woven into a long lasting fabric that could be used to make clothing, sheets and other products. Constant use would make the fabric softer. Linen could also be woven with wool to make "linsey-woolsey" fabric used in clothing.
The shorter, more coarse fibers left in the hatchels called "tow", were sometimes spun into a coarser thread and woven into towels and feed sacks. The tow was also twisted into rope.
Working with flax was a complicated process the whole family was involved in, and children began to learn at a very early age the skills needed to produce all that was needed for the family use.
Bobbin winders look very similar to the great wheels and are often mistaken for them since they usually have a table and a drive wheel. Look carefully and you will see that the table is shorter, the drive wheel is smaller, and the treadle is missing. There is also a handle on the wheel spoke.
Bobbin winders (also called quillers or spool winders) were used in two ways. First handspun skeins of yarn were transferred to spools or bobbins to be wound into a warp. Second, after the warp is on the loom and ready to be woven, yarn for filler or weft (also called woof) was wound onto quills [or spools] that fit into the boat-shaped shuttles.
Resource: Florence Feldman-Wood's article: The Spinning Wheel Sleuth
A Brief History of Weaving
Weaving is the systematic interlacing of two or more sets of elements usually, but not necessarily, at right angles, to form a coherent structure. No one knows when or where the weaving process actually began, but as far back as there are relics of civilized life, it is thought that weaving was a part of developing civilizations. Because of the perishable nature of textile goods, information found about the beginning stages of weaving is sketchy, and tracing the development of textiles is a difficult task and a tremendous challenge. Due to nature's hazards of erosion, climatic conditions, insects, and fire, few examples of early woven fabrics survived. Therefore, much of what is written about primitive weaving is based on speculation. There are, however, certain circumstances under which remnants of fabrics have survived: arid regions, bog lands, sealed tombs, and extremely cold areas. Because of these artifacts, we are fortunate to have some examples of early textiles and weaving tools.Archeologists believe that basket making and weaving were probably the first "crafts" developed by humans. Once primitive people learned ways of creating a woven structure, the possibilities were endless: netting, coverings for huts, containers for goods, carriers for the young, rugs, blankets, hammocks, pouches, body coverings. Along with our ancestors' ongoing quest for survival, there is evidence of an unconstrained desire by humans to embellish the objects created. The use of natural dyes on reeds or the combination of varying sizes and colors of weaving elements to create patterns, was likely an an attempt to express individualism and an aesthetic sensibility. Human beings naturally have a strong compulsion to be creative, and our records show that this trait was prevalent in our ancestors' lives thousands of years ago.
Research indicates that cultures on every continent devised crude looms and methods of making webs, and further study tells that us there was great similarity in the looms constructed and in the weavings produced.
The Art and History of Weaving
By Susan C. Wylly, Professor of Art, Georgia College & State University
The Prehistoric Origins of Weaving
With modern sophisticated methods of radiocarbon testing and DNA testing, today's scientists are much better able to assign accurate dates to archeological findings than they were even a decade ago. The exact date of the first hand-woven works, however, continues to remain a mystery. Nevertheless, there is evidence of cloth being made in Mesopotamia and in Turkey as far back as 7000 to 8000 BC.From: The Art and History of Weaving
By Susan C. Wylly, Professor of Art, Georgia College & State University
Carding
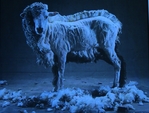
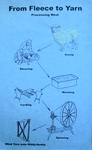
Carding: The wool is placed in small handfuls on the wire teeth of the cards, then one card is pulled across the other, brushing the wool free of dirt and tangles. The wool is then removed form the cards and rolled into a rolag.
Weaving in China
The Art and History of Weaving
By Susan C. Wylly, Professor of Art, Georgia College & State University
An era of Great change: 1820-1850
Reform & religion: The spinning wheel
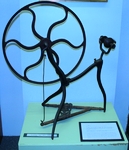
Cast Iron Spinning Wheel c. 1880
From the collection of Carl StickneyPatent for a wheel designed in Ottawa, Canada, September 3, 1880. Second patent was issued July 1883 to a manufacturer in St. Hyacinthe, Quebec, Canada.
As of 2006 only four surviving wheels existed in North America; this one makes five!
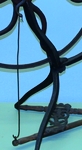
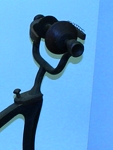